分析丨如何看待智能制造与风电制造业的转型?
上世纪80年代以来,中国制造业乘着改革的春风快速发展,通过30多年的努力,已取得了惊人的成就。这期间,中国制造业主要经历了三大阶段:第一阶段:20世纪80年代,改革开放与经济体制改革促进中国制造业高速发展
上世纪80年代以来,中国制造业乘着改革的春风快速发展,通过30多年的努力,已取得了惊人的成就。这期间,中国制造业主要经历了三大阶段:
第一阶段:20世纪80年代,改革开放与经济体制改革促进中国制造业高速发展,社会劳动力等生产要素开始活跃;
第二阶段:20世纪90年代,装备现代化大大提升生产效率,规模化经济开始发展,由改革开放初期的初级产品为主向工业制成品转变;
第三阶段:21世纪以来,设计、工艺、管理模式创新开始带动制造业升级,信息化与工业化融合改变着制造业从底层控制到高层管理的方方面面,带动产业创新和信息化发展。
目前中国已由初级产品出口国发展成为制成品大国,全球使用的手机中有70%在中国生产,80%的空调来自于中国,91%的PC也是在中国生产。通过国际贸易,中国逐步融入全球国际分工体系之中,成为其中不可分割的一个部分。中国制造业通过利用外资有了长足的发展,产业结构由劳动密集型向资本、技术密集型转变。同时,外商投资的产业链不断延伸,配套规模不断扩大,研发机构也逐渐增多。
中国是制造业大国,但还远非制造业强国,随着内部和外部环境的不断变化,中国的制造业也面临着巨大的挑战。从世界品牌实验室 2015 年发布的数据统计来看,在“世界品 牌 500 强”中,中国的企业也仅占 6%;中国汽车工业迄今为止所掌握的核心零部件技术还不到 20%。这就要提到微笑曲线(见图1),将产业链分为研发与设计、生产与制造、营销与服务三个区间,可以看到,生产制造环节处在产业链低利润环节,而两端为高端位置,为高利润环节。目前我国大部分制造业还处在国际产业价值链的低端环节,存在创新能力不强、核心竞争力不足、产业集中度低、低端产品生产扩张过度而高附加值产品依赖进口等问题。
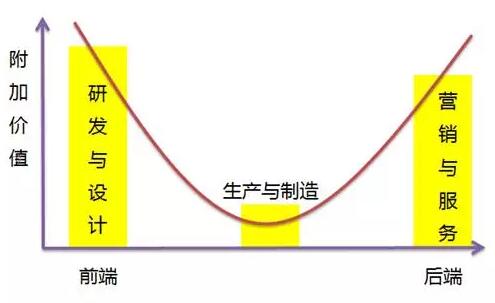
随着数字经济时代的到来,全球制造业正在发生着深刻的变革。传统的大批量、少批次的生产方式正逐步向小批量、定制化的柔性生产发展,不断满足消费者对个性化的追求。以云计算、大数据、移动互联网、物联网和人工智能等为代表的新技术飞速发展,使传统的制造企业面临前所未有的变革压力,同时产生了创新的新机遇。中国制造业如何能够面对这次颠覆性的产业革命,跟上世界变化的步伐并实现弯道超车,成为全球制造业的领先者呢?
《中国制造 2025》给出了答案,这就是制造业转型升级的国家战略。在这一战略框架下,处在不同发展阶段的制造企业需要重新认识趋势与环境,找准自己的方向,循序渐进地进行企业数字化转型、服务化创新,最终实现智能化产业升级。
智能制造的发展趋势
2013年4月,在德国工程院、弗劳恩霍夫协会、西门子公司等德国学术界和产业界的建议和推动下,德国联邦教研部与联邦经济技术部推出了《高技术战略2020》提出了“工业4.0”项目,以支持工业领域新一代革命性技术的研发与创新,升级德国的工业体系。
回顾工业革命的发展可以看出,18世纪末的第一次工业革命是由水和蒸汽为机械提供动力,即工业1.0; 19世纪末的第二次工业革命是由电力为大规模生产提供动力,即工业2.0;20世纪70年代初的第三次工业革命是基于信息技术实现自动化生产,即工业3.0;工业4.0可以理解为以智能制造为主导的第四次工业革命,旨在通过充分利用信息通讯技术和网络物理系统等手段,将制造业向智能化转型。
德国工业4.0战略的核心是一个网络、两大主题和三项集成。一个网络是信息物理系统网络(CPS),使物理系统具有计算、通信、精确控制、远程协作和自治功能。两大主题是“智能工厂”和“智能生产”,重点研究智能化基础设施和先进技术应用于整个工业生产过程,从而形成高度灵活、个性化、网络化的产业链。三项集成是“横向集成”、“纵向集成”和“端对端”:横向集成是企业之间通过价值链以及信息网络实现无缝合作,纵向集成是基于未来智能工厂中网络化的制造体系实现柔性个性化定制生产,端对端是在所有终端数字化的前提下实现的基于价值链与不同公司之间的一种整合。
目前经测算,德国工业平均达到工业3.5水平左右。德国提出的工业4.0,是在已经实现高水平的工业自动化和高质量的工业基础上,通过结合信息化技术和互联网应用,实现智能化生产来满足未来人们越来越多的个性化需求。其目的就是为了保持德国在全球的领先地位,“确保德国制造的未来”。
目前中国刚刚初步实现工业化,还远未达到工业3.0水平,比较优秀的中国制造企业也只能达到工业2.7水平。中国初步建立了完整的工业体系,正在向工业现代化大步前进,所以德国的工业4.0只能是我们的一个参考,不能完全照搬。目前我国政府和专家已充分认识到这个问题,提出了“工业2.0补课、工业3.0普及、工业4.0示范”的观点。同时国家也及时提出了“中国制造2025”战略规划,在十大领域制定了发展计划。通过三步走实现制造强国的战略目标:
到2020年,基本实现工业化,制造业大国地位进一步巩固;
到2035年,我国制造业整体达到世界制造强国阵营中等水平;
新中国成立一百年时,制造业大国地位更加巩固,综合实力进入世界制造强国前列。
风电制造业的智能转型
风电制造业,是一个绿色产业与传统工业相结合的、年轻的新能源行业。既结合了先进的产品设计,又依赖于传统工业生产。那么在新一代工业革命浪潮的冲击下,风电制造业应该如何应对并实现智能转型呢?
首先,风电制造业企业应根据自身的特点,制定一条符合企业自身发展水平的技术路线。不能求大求全,要循序渐进,从不同环节制定不同突破点,以点带面,逐步实现智能制造。
其次,作为工业制造业,产品质量是一切发展的基础。低质量的高数量是一种浪费,低质量的智能制造是无用的。只有高质量的产品才是企业生存的基石,高质量的智能制造才是产业转型的目标。因此,需要通过采用先进技术帮助提升产品质量,作为智能制造的切入点。
第三,智能制造前期的设备和研发资金投入巨大,要量力而为,同时要做好成本测算,做到最佳性价比的智能制造。
以下是从风电制造业的设计研发、生产制造、物流运输、现场运维等四个方面初步设想的一种转型方案:
一、设计研发
一是建立基于云端的广域协同研发平台,将客户、供应商、内外部设计团队纳入到一体化开发平台当中,实现从需求到产品的同步协作开发,提升产品开发速度,实现产品的精准投放。
二是设计智能风电产品,包括智能的部件和智能的风机。智能部件是智能风机的基础,也是实现智能制造的基础,通过现场总线和工业以太网与风机的主控系统联网,实现风机的物联系统网络。智能部件应带有二维码、传感器和控制器,可实现自诊断和监测,并可提供产品参数信息、生产信息、质保信息、运行信息、故障信息等。
三是在设计开发中采用信息化技术,形成风机全生命周期中所有专业研发要素的统一的多学科信息化管理系统,管理各专业图纸、工艺和材料信息、风机特性类数据及其生成过程,并能集成程序设计与管理、仿真、优化、创新、质量等工具,进行风机智能研发,快速提升研发效率,统一管理数据源。
二、生产制造
一是提升生产自动化水平。目前风力发电机组还是以人工装配为主,效率低、质量管控难度大,人员素质和责任心对质量影响大。通过在关键工艺引入自动化和智能设备,提升产品制造质量和效率。如轴承螺栓自动化锁紧装置,传动链自动进给装配、螺栓润滑剂自动涂抹装置等。
二是引入制造执行系统(MES),实现生产信息管理及调度的智能化,包括智能部件入库信息录入自动化,生产过程信息的实时记录和存储,生产排产的柔性调度,生产工艺文件的发布、变更等智能管理,生产数据及报表的自动生成,从而大大提高整个制造过程的管理水平和管理效率。
三、物流运输
物流运输过程由于时间长、地点分散及外包等原因,一直是管理难点。特别是叶片等大部件运输,产品超大超长,运输过程中易出现损伤,同时存在私自维修的现象,难以进行监控。维修不合格的叶片运行中易出现损坏,给业主和整机厂家带来重大经济损失。通过智能技术可以在运输时安装基于云存储的GPS智能监控模块,可以将运输车辆的位置、速度、加速度、振动等运输参数和影像资料定时上传到云平台,自动生成数据图表,实现对运输过车的监控及可追溯性,实现智能化监督。
四、现场运维
由于风场现场分散、对现场安装和运维质量的监督难度较大。
一是通过引入基于云平台的智能摄像设备,可实现安装现场和风机定检维护过程进行实时记录和存储,实现过程的可追溯性,提升管理水平。
二是风机产品智能化,依托智能化部件的自诊断功能和风机智能化故障信息分析,实现风机故障的精准定位。
三是建立依托云平台的运行维护系统,所有在运风机运行数据接入云平台,进行大数据收集和分析,掌握不同地区风机的运行情况,调整运行策略,支持现场故障快速处理,提供产品改进方向,提高风场效益,实现风场的智能化管理。
原标题:分析丨智能制造与风电制造业转型

责任编辑:lixin
免责声明:本文仅代表作者个人观点,与本站无关。其原创性以及文中陈述文字和内容未经本站证实,对本文以及其中全部或者部分内容、文字的真实性、完整性、及时性本站不作任何保证或承诺,请读者仅作参考,并请自行核实相关内容。
我要收藏
个赞
-
重新审视“双循环”下的光伏行业
2020-11-02光伏行业,光伏技术,光伏出口 -
能源转型进程中火电企业的下一程
2020-11-02五大发电,火电,煤电 -
国内最高额定水头抽蓄电站2#引水上斜井滑模混凝土施工顺利完成
2020-10-30抽水蓄能电站,长龙山抽水蓄能电站,水力发电
-
能源转型进程中火电企业的下一程
2020-11-02五大发电,火电,煤电 -
资本市场:深度研究火电行业价值
2020-07-09火电,火电公司,电力行业 -
国家能源局印发2020年能源工作指导意见:从严控制、按需推动煤电项目建设
2020-06-29煤电,能源转型,国家能源局
-
高塔技术助力分散式风电平价上网
2020-10-15分散式风电,风电塔筒,北京国际风能大会 -
创造12项世界第一!世界首个柔性直流电网工程组网成功
2020-06-29 清洁能源,多能互补,风电 -
桂山风电项目部组织集体默哀仪式
2020-04-08桂山风电项目部组织
-
国内最高额定水头抽蓄电站2#引水上斜井滑模混凝土施工顺利完成
2020-10-30抽水蓄能电站,长龙山抽水蓄能电站,水力发电 -
今后秦岭生态环境保护区内不再审批和新建小水电站
2020-06-29小水电,水电站,水电 -
3.2GW!能源局同意确定河北新增三个抽水蓄能电站选点规划
2020-06-29抽水蓄能,抽水蓄能电站,国家能源局
-
重新审视“双循环”下的光伏行业
2020-11-02光伏行业,光伏技术,光伏出口 -
官司缠身、高层动荡、工厂停产 “保壳之王”天龙光电将被ST
2020-09-11天龙光电,光伏设备,光伏企业现状 -
央视财经热评丨光伏发电的平价时代到了吗?
2020-08-24储能,光伏储能,平价上网